2002 – 2011
2008: QForm 5.0
New performance and versatile features. New QForm 5.0 is a versatile simulation tool. It simulates nearly all bulk metal forming processes and some related processes like heating and heat treatment. A unique user-friendly interface excludes the need for special training so that the program provides a quick return of investment.
- New licensing policy: the program performance and capabilities can be tuned on demand individually for every user according to his needs.
- No limits for complexity of simulation job – full 64-bit application running in parallel on up to 8 CPUs.
- Special module QForm-Extrusion provides unique performance for simulation of aluminum profiles of the most complicated shapes.
- Module QForm-MS provides simulation of recrystallisation and grain growth during deformation and during the pauses between forming operations.
- The program was extended to allow simulation of the following processes where the tools and/or the billet are intensively rotating (ring rolling, railroad wheel rolling, cross-wedge rolling, transversal rolling and helical rolling of tubes)
- New extended facilities for setting special boundary conditions and/or mesh size to any area of the billet or tool surface at any stage of simulation process.
- Simulation of induction heating.
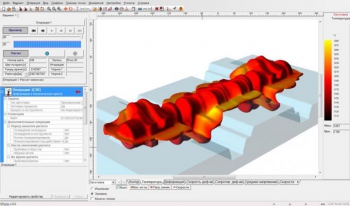
2002: QFORM3D software
Gaining the experience and improving the algorithms created prerequisites to the development of a 3D metal forming process software. This was also supported by an increasing popularity of the FORM-2D and QFORM software packages, making it possible to involve development teams from various countries in order to join the efforts for such a complex project. It was due to the efforts of the international consortium that the QFORM3D software was brought out.
Developing the 3D software it was essential to ensure an easy application, the possibility of preparing all data for the computation within a few minutes, the pursuance of the computation from the beginning to the end in an absolutely automatic mode without any user intervention and the achievement of a guaranteed accurate result, even if the user had no special knowledge in the field of the finite element simulation theory.
To achieve these goals, a few absolutely new solutions were developed and applied. Here are the key concepts:
- QFORM3D combines 2D and 3D simulation in a single software.
- The integration of 2D and 3D simulation in the same software package provides a unique opportunity to simulate efficiently the process chains comprising several forging impressions, the first of which have axial symmetry and can be solved fast in a 2D setting (e. g. upsetting and preliminary impressions) and the subsequent ones require full-scale 3D simulation.
- The effective geometry data import is provided with a reliable interface, which includes all solid body simulation systems.
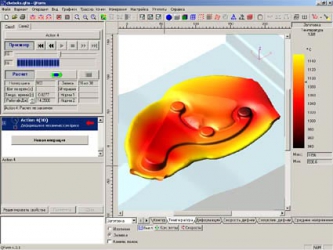