Extrusion
QForm Extrusion simulation program predicts material flow and helps estimate the quality of final production. The software is intended for simulation of any kind of profiles including solid and hollow profiles with shapes of any complexity. QForm Extrusion is the only software that takes into account the influence of die set deflection on the material flow.
Photo of the real profile
Simulation in QForm. Profile velocity field
Watch Introductory Video (YouTube)
Versatility of QForm Extrusion
QForm Extrusion is a great tool to create much faster and reliable workflow of extrusion process development as for die designers as well for extrusion units. But also, it can be used as a tool for teamwork and communication between tool and profile manufacturers.
Even if your partner plants have no QForm license you can share simulation results with them using special freeware QForm Viewer or using auto-generated reports. QForm Viewer features all tools for process analysis but cannot be used for simulation or geometry extraction.
Die set manufacturers or tool shop engineers usually do not burden themselves with velocity-temperature balance and other extrusion process-specific parameters that are very important for extrusion unit in terms of product quality and process efficiency. Simulation results sharing gives these two parties opportunity to collaborate, create reliable extrusion processes without die set trials and even to educate each other, increase overall quality of design and technology.
Here we propose several workflow schemes for different use cases of pre-manufacture die set design process. When both parties are satisfied with design solution approved by real technological parameters, die set is ready to be manufactured.
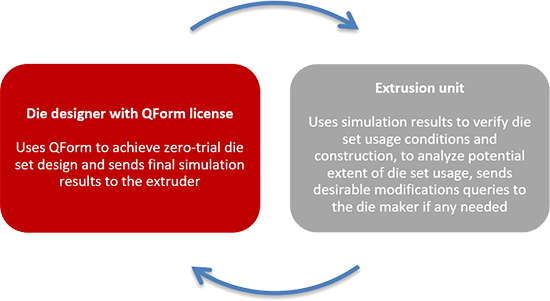
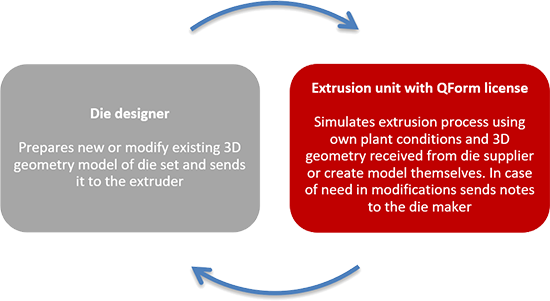
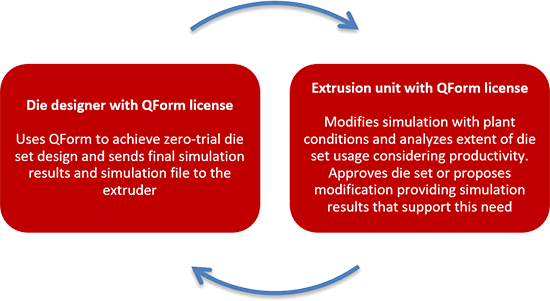