Mechanical press forging
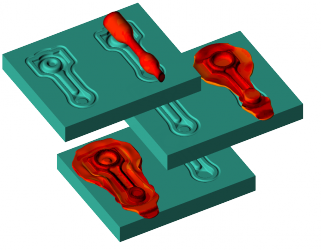
Large-scale mass production of forged parts on mechanical presses demands a highly efficient and well-designed technology for the forging process. With typical high production output, even a small reduction of the cost of each forged part gives a big economic benefit.
QForm simulation software allows users to implement experiments without wasting time or material that would be needed for shop floor testing. It helps designers check the technological processes and find optimal parameters for the workpiece as well as for the tool.
Simulation improves the efficiency of a technological process by:
- Reducing wasted material (increasing stock utilization ratio)
- Increasing the durability of the tooling (die)
- Providing favorable microstructure of the forged part (fibrous structure), to increase its operational qualities
- Providing optimal temperature profile of heating, forging and heat treatment to get favorable microstructure
Advantages
- Quick technology developing time
- Verification of the final shape of the forged part and quality of die filling
- Forged part properties prediction
- Identification of forging defects such as laps, flow-through defects, underfilled areas and excess material
- Prediction of tool life by tool stress analysis and identification of the zones that have the highest load and die wear
- Prediction of load and energy of deformation to verify the correct equipment choice
- The opportunity to see how the die cavity is filled to solve flow problems and find ways to improve the technology
- Solving problems related to production, for example checking the influence of the material quality or the quality of the surface of the machined product
Temperature distribution in the forged part simulated in QForm
Carabine forging simulation in QForm
Special QForm features that help simulate Mechanical press forging
- One of the strengths of QForm is the unique adaptive finite-element mesh generator which makes and rebuilds an optimized mesh for forgings of any complexity in a completely automatic mode. The finite-element size is optimized to be fine only in places necessary for accuracy and in other places the mesh remains large. This allows the program to make calculations quicker without loss of accuracy
- Selection of simulation step size is also automatic, ensuring the optimum balance of speed and accuracy
- The highly automatization simulation software allows the user to concentrate on the technology of forging and not worry about mesh generation algorithms and algorithms of the finite element method
- Easy setup of parameters of material, equipment and technological parameters in our special data preparation wizard
- Special optimization of the “Core” of the software for simulation of hot bulk forging technologies
- Coupled simulation task helps increase the accuracy of the simulation
- The program includes a wide range of research tools for solving of specialized tasks: special boundary conditions, control of mesh parameters and simulation step, writing of user subroutines, data import and export with external (third parties) applications
Example
The video below shows an example of forging of a connecting rod on a mechanical press. This forging technology is interesting because prior to forging, the billet is preformed by reducer rolling with 4 actions. After reducer rolling a flattening operation is used followed by two steps of forging - blocker and finish forging. The using of a reducer rolling operation as preforming allows the forging to achieve a favorable microstructure (fibrous structure) as shown in the last stage of the video.