Ring and wheel rolling
Wheel rolling simulation in QForm. Plastic strain distribution field.Ring rolling is a technological process typically used in the bearing industry due to its high precision, efficiency and performance. Due to increased use of rolled rings in industries such as energy (including wind power) and aerospace, demand is increasing for bearings and other parts produced by ring rolling including: aerospace engine components, flanges, gear sprockets, nuclear reactor parts, bearing bushes, pressure vessels shells and rope pulleys. The diameters of rolled rings can reach up to 10 meters and the directed - circumferential grain flow in seamless rolled rings is a unique property and very important advantage of the ring rolling process. Because of very high demands in accuracy and reliability required for production of ring and wheel rolling, efficient simulation is needed for detail investigation and verification in extremely high-performance finite element simulation software.
Ring rolling simulation in QForm. Ring rolling on radial-axial machine. Plastic strain distribution field.
Profiled ring rolling simulation in QForm. Ring rolling on radial-axial machine. Temperature distribution field.
With help of simulation in QForm it is possible to reduce costs for developing and setting up ring rolling technological processes as well as to provide an optimal working regime of ring rolling machines. QForm helps predict the final shape, check the technology for the presence of defects and to estimate load and torque in all tools. In the postprocessor simulation of tools, it is possible to check load gradient in the main and guide rolls and in the mandrel as well as to predict wear and deflections of the tools for a more detailed investigation of final ring shape.
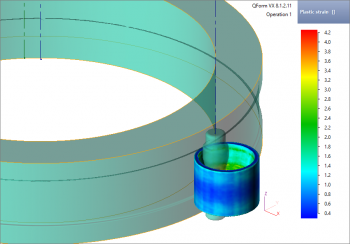
The following technological tasks are solved in QForm software during simulation of ring and wheel rolling processes:
- Control of temperatures within the process and checking for locations that exceed the specified temperature range of steel deformation for the entire technological process chain
- Prediction of grain flow quality in ring or wheel thanks to lines tracing from the preforming operation through the final rolling operation
- Evaluation of rolling curves and strategies: dependence of ring growth speed from diameter and dependence of height from thickness
- Evaluation of optimal rolling regimes
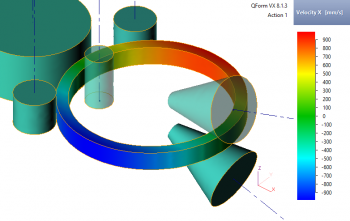
Advantages
- Comparatively fast simulation speed combined with simplicity of the user interface helps to make a few simulations of developing technology in a relatively short period of time
- Possibility to predict final ring or wheel shape with selected rolling parameters
- Macrostructure and fiber structure prediction to control fiber location on the working surface of ring
- Estimation of temperature profile of the ring and tools through the entire rolling process
- Evaluation of heating temperature and parameters of forging operations of billets before rolling
Special QForm features that help simulate ring and wheel rolling process
- Specially developed fully automated dual mesh algorithm that allows a significant increase of simulation speed of incremental processes
- Setting of rolling curves and strategies from the most popular real rolling machines such as SMS Meer, Muraro, Siempelkamp and Mitsubishi
- Special algorithm for the mesh generation in tools with highly densified mesh in contact zones with workpiece that allow for significant increases in simulation accuracy without increasing simulation time
- Possibility to simulate the whole technological chain starting from workpiece heating through performing operation, punching and finishing by rolling
- Interface to set ring rolling for various types of rolling machines such as radial, radial-axial and wheel rolling as well as rolling in case (frame).